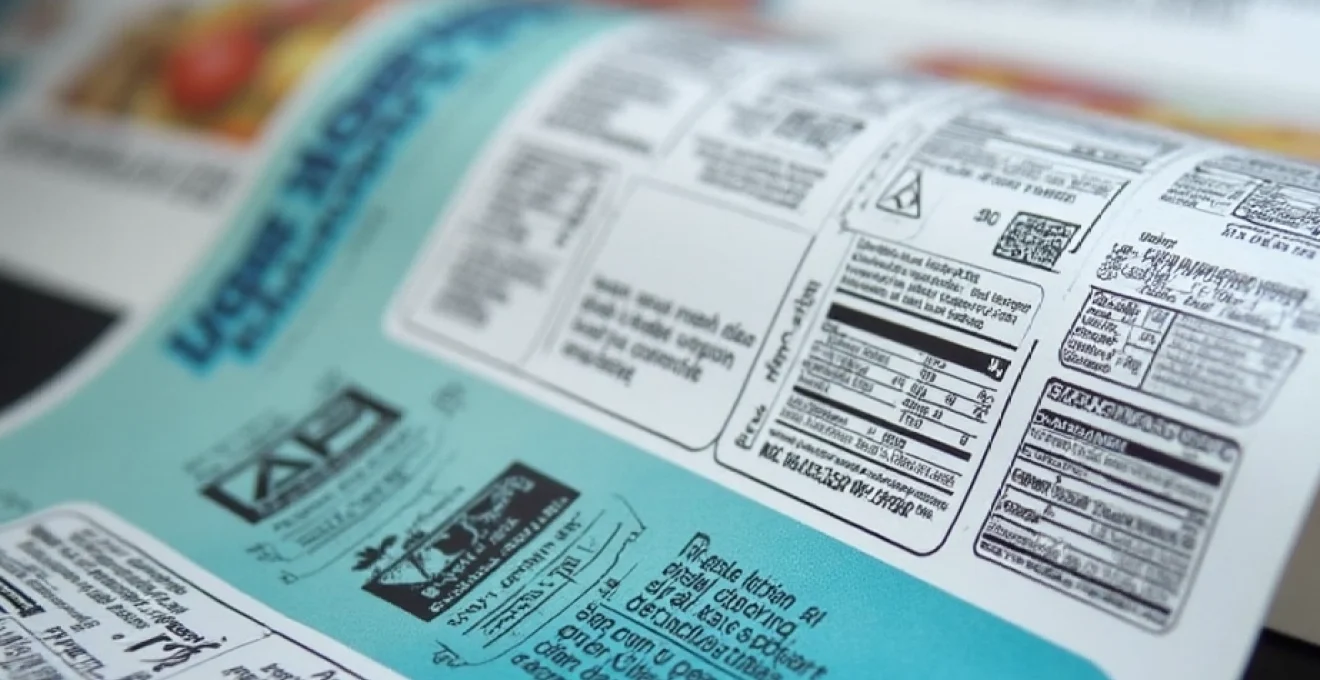
Custom label printing has revolutionized product packaging and branding across industries. From enhancing visual appeal to conveying critical information, custom labels play a pivotal role in product identification, safety compliance, and marketing strategies. As technology advances, the capabilities and applications of custom label printing continue to expand, offering businesses unprecedented flexibility and creativity in their labeling solutions.
The growing demand for personalized products and the need for efficient inventory management have further propelled the custom label printing industry forward. With a myriad of materials, printing technologies, and finishing techniques available, companies can now create labels that not only meet their specific requirements but also stand out in competitive markets.
Digital printing technologies for custom labels
Digital printing has emerged as a game-changer in the custom label industry, offering unparalleled flexibility and cost-effectiveness for short to medium print runs. Unlike traditional printing methods, digital printing eliminates the need for printing plates, significantly reducing setup time and costs. This technology allows for quick turnaround times, making it ideal for businesses that require frequent design changes or small batch productions.
One of the primary advantages of digital printing is its ability to produce high-quality, full-color labels with exceptional detail and vibrancy. Variable data printing, a feature unique to digital technology, enables the customization of individual labels within a single print run. This capability is particularly valuable for personalized marketing campaigns or serialized product tracking.
Two main types of digital printing technologies dominate the custom label market:
- Inkjet printing: Offers superior color accuracy and is suitable for a wide range of materials
- Toner-based printing: Provides excellent durability and is often used for labels requiring high resistance to environmental factors
As digital printing technology continues to advance, we’re seeing improvements in print speed, color gamut, and durability, making it an increasingly attractive option for businesses of all sizes.
Material selection for custom label durability
Choosing the right material for your custom labels is crucial for ensuring durability and performance in various environments. The selection process should consider factors such as the product’s intended use, storage conditions, and exposure to elements like sunlight, moisture, or chemicals. Let’s explore some popular label materials and their specific applications.
Polyester labels for chemical resistance
Polyester labels are renowned for their exceptional durability and resistance to chemicals, making them ideal for industrial and laboratory applications. These labels can withstand exposure to harsh solvents, acids, and oils without degrading or losing their print quality. Polyester’s dimensional stability also ensures that labels maintain their shape and size even in extreme temperatures.
Applications for polyester labels include:
- Laboratory sample identification
- Automotive parts labeling
- Industrial equipment tags
Vinyl labels for outdoor applications
Vinyl labels are the go-to choice for outdoor applications due to their excellent weather resistance and flexibility. These labels can withstand prolonged exposure to UV rays, rain, and temperature fluctuations without fading or peeling. Vinyl’s conformability allows it to adhere well to curved or irregular surfaces, making it versatile for various product types.
Common uses for vinyl labels include:
- Outdoor equipment identification
- Vehicle graphics and decals
- Weatherproof warning signs
Paper labels for cost-effective short-term use
While not as durable as synthetic materials, paper labels remain a popular choice for short-term applications or products with a limited shelf life. They offer a cost-effective solution for high-volume printing and are easily recyclable, aligning with eco-friendly packaging initiatives. Coated paper variants can provide improved moisture resistance and print quality for more demanding applications.
Typical uses for paper labels include:
- Food and beverage packaging
- Shipping and mailing labels
- Temporary promotional stickers
BOPP labels for moisture resistance
Biaxially Oriented Polypropylene (BOPP) labels offer excellent moisture resistance and clarity, making them ideal for applications where label appearance is crucial. These labels maintain their integrity in humid environments and provide a “no-label” look when applied to clear containers. BOPP’s durability and attractive finish make it a popular choice in the food and beverage industry.
Key applications for BOPP labels include:
- Bottled water and beverage labeling
- Cosmetics packaging
- Health and beauty product labels
Advanced finishing techniques in custom label production
The finishing process plays a crucial role in enhancing the visual appeal and functionality of custom labels. Advanced finishing techniques can transform a simple label into a powerful branding tool, adding texture, depth, and protective properties. These techniques not only improve aesthetics but can also contribute to the label’s durability and performance.
UV coating for enhanced gloss and protection
UV coating is a popular finishing technique that applies a clear, glossy layer to the label surface. This coating is cured instantly using ultraviolet light, resulting in a high-shine finish that enhances color vibrancy and provides protection against scuffs and moisture. UV coating can be applied selectively to create contrast between matte and glossy areas, adding visual interest to the label design.
UV coating can increase the label’s resistance to fading, extending its lifespan in challenging environments.
Embossing and debossing for tactile branding
Embossing and debossing techniques create raised or recessed areas on the label surface, adding a tactile element to the branding. These processes can be used to highlight logos, text, or design elements, creating a premium look and feel. When combined with foil stamping, embossing can produce striking metallic raised effects that catch the eye and elevate the perceived value of the product.
Hot foil stamping for metallic accents
Hot foil stamping applies a thin layer of metallic foil to specific areas of the label using heat and pressure. This technique creates brilliant, reflective accents that can significantly enhance the label’s visual appeal. Foil stamping is often used for luxury product packaging, adding a touch of elegance and sophistication to the label design.
Die-cutting for unique label shapes
Die-cutting allows for the creation of custom label shapes and sizes, moving beyond traditional rectangular or circular designs. This technique can be used to create intricate cutouts, rounded corners, or entirely unique shapes that complement the product packaging. Die-cut labels can help products stand out on crowded shelves and reinforce brand identity through distinctive shapes.
Industry-specific custom label applications
Custom label printing finds diverse applications across various industries, each with its unique requirements and regulations. Understanding these specific needs is crucial for creating effective labeling solutions that comply with industry standards while meeting branding objectives.
GHS-compliant labels for chemical industry
The chemical industry requires labels that adhere to the Globally Harmonized System (GHS) of Classification and Labeling of Chemicals. These labels must include standardized pictograms, hazard statements, and precautionary information. Custom GHS labels need to be durable enough to withstand exposure to chemicals and remain legible throughout the product’s lifecycle.
Tamper-evident labels for pharmaceutical packaging
In the pharmaceutical industry, tamper-evident labels play a critical role in ensuring product safety and authenticity. These labels are designed to show visible signs of tampering, helping to protect consumers and maintain the integrity of medical products. Custom tamper-evident labels can incorporate various security features such as holograms, void patterns, or serialized codes.
Temperature-sensitive labels for food safety
The food industry utilizes temperature-sensitive labels to monitor and ensure food safety during transportation and storage. These labels change color or reveal hidden text when exposed to temperatures outside the safe range. Custom temperature-sensitive labels can be tailored to specific temperature thresholds and integrated with existing packaging designs.
RFID-enabled labels for retail inventory management
Retail businesses are increasingly adopting RFID-enabled labels for improved inventory management and theft prevention. These labels contain embedded RFID chips that can be scanned from a distance, allowing for quick and accurate stock tracking. Custom RFID labels can be designed to blend seamlessly with product packaging while providing valuable data for supply chain optimization.
Quality control measures in custom label printing
Maintaining consistent quality in custom label production is essential for ensuring customer satisfaction and compliance with industry standards. Implementing robust quality control measures throughout the printing process helps identify and address issues before they reach the end-user. Key aspects of quality control in custom label printing include:
- Color management systems to ensure accurate and consistent color reproduction
- Automated inspection systems for detecting print defects and registration errors
- Material testing to verify adhesive performance and substrate compatibility
- Regular calibration of printing equipment to maintain optimal performance
Advanced quality control technologies, such as spectrophotometers and vision systems, play a crucial role in maintaining high standards in label production. These tools enable real-time monitoring and adjustment of print parameters, ensuring consistency across large print runs.
Integration of custom labels with packaging automation systems
As manufacturing processes become increasingly automated, the integration of custom label printing with packaging automation systems has become a key focus for many industries. This integration streamlines production, reduces errors, and improves overall efficiency in the packaging process.
Label applicators forhigh-speed production lines
Automated label applicators are designed to apply custom labels to products or packaging at high speeds with precision. These systems can handle various label sizes and shapes, adapting to different product configurations. Advanced label applicators can apply labels to multiple sides of a product in a single pass, significantly increasing production throughput.
Print-and-apply systems for real-time customization
Print-and-apply systems combine on-demand label printing with automated application, allowing for real-time customization of labels during the packaging process. This technology is particularly valuable for industries requiring variable data printing, such as logistics and e-commerce, where shipping labels need to be generated and applied dynamically.
Vision systems for label placement verification
Vision systems play a critical role in ensuring accurate label placement and quality control in automated packaging lines. These systems use cameras and image processing software to verify label position, orientation, and print quality in real-time. Any deviations from set parameters can trigger alerts or automated corrections, maintaining high standards of labeling consistency.
The integration of custom label printing with packaging automation not only improves efficiency but also opens up new possibilities for personalization and traceability in product packaging. As these technologies continue to evolve, we can expect to see even more sophisticated and flexible labeling solutions that cater to the dynamic needs of modern manufacturing and distribution processes.