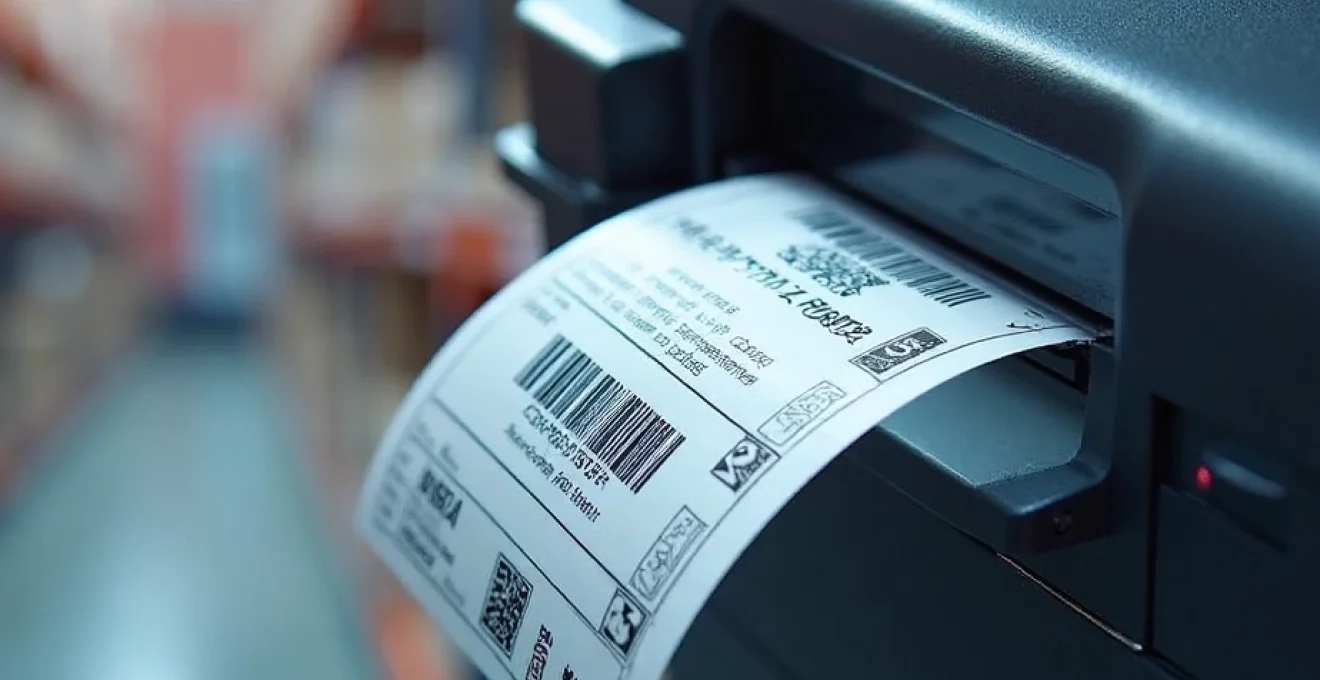
Thermal printing technology has revolutionized the logistics industry, offering unparalleled speed, efficiency, and reliability in label production. As supply chains become increasingly complex and demanding, the role of efficient labeling cannot be overstated. Thermal printers have emerged as a cornerstone technology, enabling rapid throughput, accurate tracking, and seamless integration with warehouse management systems. Their ability to produce high-quality, durable labels without the need for ink or toner has made them indispensable in modern logistics operations.
Thermal printing technology in logistics operations
At its core, thermal printing utilizes heat to create images on specially designed paper or labels. This process eliminates the need for traditional ink or toner, resulting in a more streamlined and cost-effective printing solution. In logistics, where speed and accuracy are paramount, thermal printers offer a significant advantage over conventional printing methods. They can produce labels, barcodes, and shipping documents at a rate that keeps pace with the fast-moving nature of warehouses and distribution centers.
The efficiency of thermal printers in logistics stems from their ability to generate clear, scannable barcodes and text that remain legible even in challenging environments. This reliability is crucial for maintaining accurate inventory tracking and ensuring that packages reach their intended destinations without delays caused by unreadable labels. APS Printers have been at the forefront of developing thermal printing solutions tailored specifically for the logistics sector, recognizing the unique demands of this industry.
Direct thermal vs. thermal transfer printing methods
When it comes to thermal printing in logistics, two primary methods dominate the field: direct thermal and thermal transfer. Each has its own set of advantages and is suited to different applications within the supply chain. Understanding the differences between these methods is crucial for selecting the right printing solution for specific logistics needs.
Heat-sensitive paper mechanisms in direct thermal printing
Direct thermal printing operates by applying heat directly to chemically treated, heat-sensitive paper. When the thermal printhead heats specific areas of the paper, it turns black, creating the desired image or text. This method is particularly efficient for short-term labeling needs, such as shipping labels or receipts, where the lifespan of the label is relatively brief.
The simplicity of direct thermal printing makes it an attractive option for high-volume logistics operations. With no ink or ribbons to replace, maintenance is minimal, and the printing process is faster. However, the heat-sensitive nature of the labels means they can fade over time, especially when exposed to heat or direct sunlight.
Ribbon-based thermal transfer process for durable labels
Thermal transfer printing, on the other hand, uses a heated printhead to melt a wax or resin coating from a ribbon onto the label material. This method produces more durable labels that can withstand exposure to chemicals, moisture, and abrasion. For logistics operations that require long-lasting labels, such as asset tracking or outdoor use, thermal transfer is often the preferred choice.
While thermal transfer printers require the additional step of ribbon replacement, they offer greater flexibility in terms of label materials and enhanced durability. This makes them ideal for creating labels that need to withstand the rigors of long-term storage or transportation in harsh conditions.
Comparative analysis of print longevity and environmental resistance
When comparing direct thermal and thermal transfer printing, longevity and environmental resistance are key factors to consider. Direct thermal labels are more susceptible to fading and discoloration when exposed to heat, light, or certain chemicals. This can be problematic for items that may be stored for extended periods or transported through various environmental conditions.
Thermal transfer labels, conversely, offer superior resistance to environmental factors. The printed image is effectively “baked” onto the label surface, providing greater protection against fading, smudging, and chemical exposure. This durability makes thermal transfer labels the go-to choice for applications where label integrity is critical over long periods.
The choice between direct thermal and thermal transfer printing in logistics often comes down to balancing the need for durability against the desire for simplicity and cost-effectiveness in high-volume operations.
Key components of thermal printers for logistics applications
To understand how thermal printers achieve their efficiency in logistics, it’s essential to examine their key components. Each element plays a crucial role in ensuring fast, accurate, and reliable label production.
Thermal printheads: DPI resolution and printing speed
The thermal printhead is the heart of any thermal printer. It consists of a row of heating elements that create the image on the label. The resolution of a printhead is measured in dots per inch (DPI), with higher DPI values resulting in sharper, more detailed prints. For logistics applications, a balance between resolution and speed is crucial.
Typical resolutions for logistics thermal printers range from 203 DPI for standard shipping labels to 300 DPI or higher for smaller barcodes or detailed graphics. The printhead’s ability to heat up and cool down rapidly directly affects printing speed, with some high-end models capable of producing hundreds of labels per minute.
Media sensors for label detection and positioning
Accurate label positioning is critical in logistics to ensure that barcodes and text are printed in the correct location for easy scanning and reading. Media sensors in thermal printers detect the edges of labels, gaps between labels, and pre-printed marks to ensure precise alignment.
Advanced sensors can also adjust for variations in label size and type, allowing for greater flexibility in the types of media that can be used. This adaptability is particularly valuable in logistics environments where different label formats may be required for various products or shipping methods.
Platen rollers and paper feed mechanisms
The platen roller works in conjunction with the printhead to ensure smooth and consistent label feeding. It provides the necessary pressure to maintain contact between the label and the printhead, crucial for achieving uniform print quality across the entire label surface.
Efficient paper feed mechanisms are essential for maintaining high printing speeds without jams or misalignments. Many modern thermal printers designed for logistics use feature auto-loading capabilities and adjustable guides to accommodate different label widths and types, minimizing setup time and reducing the risk of errors.
Integrated circuit boards for print control and connectivity
The brains of a thermal printer reside in its integrated circuit boards. These components control all aspects of the printing process, from interpreting print commands to managing the precise timing of printhead heating elements. In logistics applications, the processing power of these boards is particularly important for handling complex label designs and high-volume print jobs.
Modern thermal printers also incorporate advanced connectivity options, including Ethernet, Wi-Fi, and Bluetooth capabilities. These features allow for seamless integration with warehouse management systems and enable remote printing and monitoring, essential for distributed logistics operations.
Efficiency factors in thermal printing for supply chain management
The efficiency of thermal printers in logistics extends beyond mere print speed. Several factors contribute to their overall effectiveness in supply chain management, making them an indispensable tool for modern warehouses and distribution centers.
High-speed printing capabilities for warehouse throughput
In high-volume logistics environments, the ability to produce labels quickly is paramount. Thermal printers excel in this area, with many models capable of printing several inches per second. This high-speed capability ensures that labeling processes keep pace with picking, packing, and shipping operations, preventing bottlenecks in the supply chain.
The speed advantage of thermal printers is particularly evident in e-commerce fulfillment centers, where rapid order processing is critical. By minimizing the time spent waiting for labels, these printers contribute significantly to improving overall warehouse throughput and meeting tight shipping deadlines.
Energy consumption and heat management in continuous operations
Despite their reliance on heat for printing, modern thermal printers are designed with energy efficiency in mind. Advanced power management systems ensure that the printer only consumes energy when actively printing, reducing electricity costs and environmental impact.
Effective heat management is crucial for maintaining consistent print quality and extending the life of the printhead. Thermal printers used in logistics often incorporate cooling systems and temperature sensors to prevent overheating during long print runs, ensuring reliable performance even in 24/7 operations.
Barcode and QR code generation for inventory tracking
One of the most critical functions of thermal printers in logistics is the generation of accurate, easily scannable barcodes and QR codes. These codes are the linchpin of modern inventory tracking systems, enabling real-time visibility of products throughout the supply chain.
Thermal printers excel at producing crisp, high-contrast barcodes that can be reliably scanned even in low-light warehouse environments. The ability to quickly generate and print custom barcodes on demand allows for flexible inventory management and reduces the need for pre-printed label stock.
Integration with warehouse management systems (WMS)
The true efficiency of thermal printers in logistics is realized through their seamless integration with warehouse management systems. Modern thermal printers support a wide range of communication protocols and data formats, allowing them to receive print jobs directly from WMS software.
This integration enables automated label printing triggered by events within the WMS, such as order picking or inventory movement. By eliminating manual data entry and reducing the risk of labeling errors, integrated thermal printing solutions contribute significantly to the overall accuracy and efficiency of logistics operations.
The synergy between thermal printers and warehouse management systems creates a powerful ecosystem for streamlined logistics, where every label printed represents a data point in the broader supply chain narrative.
Advancements in thermal printer connectivity for logistics
As logistics operations become increasingly digital and interconnected, the connectivity features of thermal printers have evolved to meet new demands. These advancements are playing a crucial role in enhancing the flexibility and efficiency of labeling processes across diverse supply chain environments.
Wireless and bluetooth printing solutions for mobile workflows
The advent of wireless and Bluetooth-enabled thermal printers has revolutionized mobile workflows in logistics. These portable devices allow warehouse staff to print labels on the spot, eliminating the need to return to a fixed printing station. This mobility is particularly valuable in large warehouses or outdoor logistics yards where flexibility is key.
Wireless thermal printers enable real-time label generation based on current inventory data, reducing errors and improving efficiency. They also facilitate the implementation of dynamic slotting strategies, where product locations can be optimized on the fly, with new location labels printed as needed.
Cloud-based print management in distributed logistics networks
Cloud-based print management solutions are transforming how logistics companies handle label printing across multiple locations. These systems allow for centralized control and monitoring of thermal printers across an entire network of warehouses and distribution centers.
With cloud-based management, logistics managers can remotely update label templates, monitor printer status, and track usage across all connected devices. This centralized approach ensures consistency in labeling across the entire supply chain and enables rapid deployment of changes to meet new regulatory requirements or customer needs.
API integration for automated label generation from ERP systems
The integration of thermal printers with enterprise resource planning (ERP) systems through APIs represents a significant leap forward in automation. This integration allows for direct communication between business systems and printing hardware, enabling fully automated label generation based on real-time data.
For example, when an order is processed in the ERP system, it can automatically trigger the printing of shipping labels, packing lists, and customs documentation without any manual intervention. This level of automation not only increases efficiency but also reduces the risk of errors associated with manual data entry.
Thermal printer maintenance and optimization in High-Volume environments
To maintain the efficiency of thermal printers in demanding logistics environments, proper maintenance and optimization practices are essential. These practices ensure consistent print quality, minimize downtime, and extend the lifespan of the printing equipment.
Printhead cleaning protocols for consistent print quality
Regular cleaning of the thermal printhead is crucial for maintaining print quality and preventing premature wear. In high-volume logistics operations, printheads can accumulate dust, adhesive residue, and other debris that can affect print clarity and potentially damage the printhead.
Establishing a routine cleaning protocol using appropriate cleaning materials is essential. Many thermal printer manufacturers recommend cleaning the printhead after every roll of media or at regular intervals based on print volume. This proactive maintenance approach can significantly extend the life of the printhead and ensure consistent print quality.
Media selection and storage for optimal thermal transfer
The choice of label media and its proper storage are critical factors in thermal printer performance. Using high-quality, compatible media ensures optimal print quality and reduces wear on the printhead. In logistics applications, where labels may be exposed to various environmental conditions, selecting the appropriate media type is crucial for label durability.
Proper storage of thermal media is equally important. Exposure to heat, humidity, or direct sunlight can degrade the thermal coating on labels, leading to poor print quality or premature fading. Implementing proper storage practices and inventory rotation for thermal media can help maintain consistent print quality and reduce waste.
Firmware updates and performance tuning for extended printer lifespan
Regular firmware updates are essential for maintaining the performance and security of thermal printers in logistics operations. These updates often include improvements to print speed, connectivity, and compatibility with new label formats or barcode standards.
Performance tuning, such as adjusting print darkness and speed settings, can optimize print quality while minimizing wear on printer components. Regular calibration of media sensors ensures accurate label positioning and reduces the risk of printing errors.
By implementing these maintenance and optimization practices, logistics operations can ensure that their thermal printers continue to operate at peak efficiency, supporting the demanding requirements of modern supply chain management. Regular maintenance not only extends the lifespan of the printing equipment but also contributes to overall operational efficiency by reducing unexpected downtime and maintaining consistent print quality.