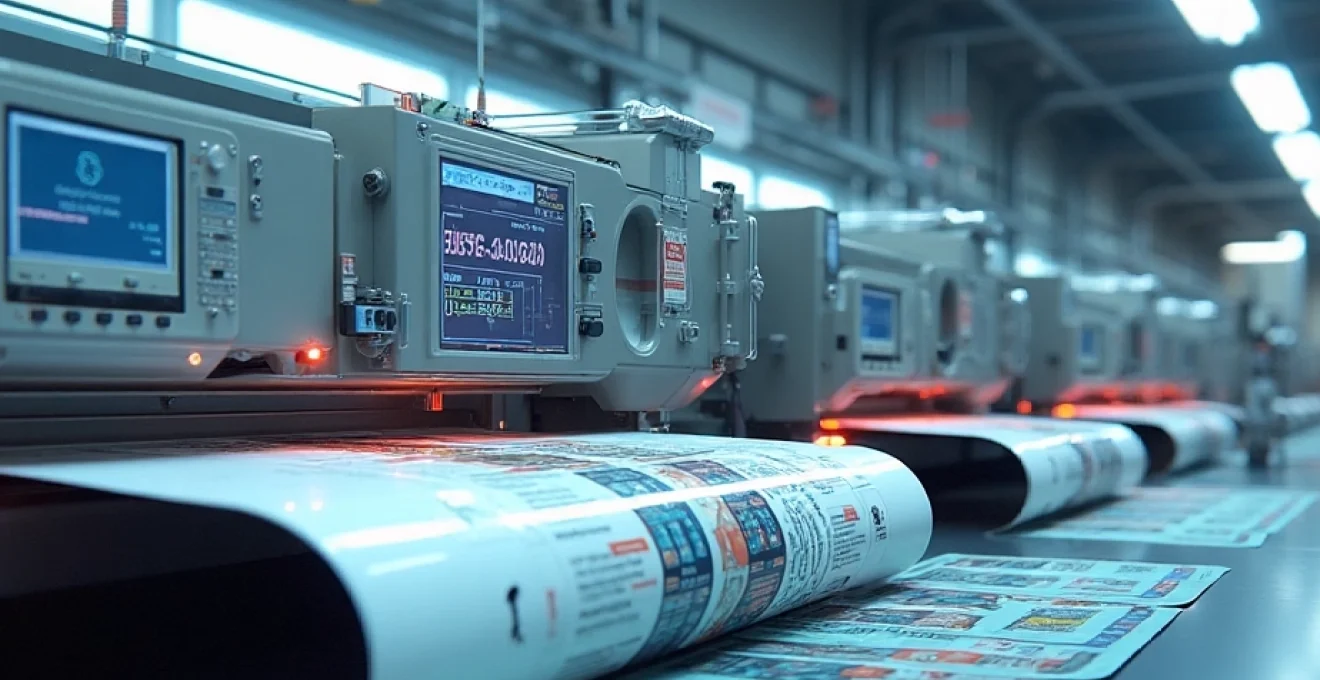
The world of industrial printing for packaging and labeling is evolving rapidly, driven by technological advancements and changing market demands. From high-volume flexographic printing to cutting-edge digital inkjet systems, manufacturers now have a wide array of options to create eye-catching, functional, and sustainable packaging solutions. This comprehensive overview explores the latest innovations in industrial printing technologies, their applications, and the impact they’re having on the packaging and labeling industry.
Flexographic printing technology for high-volume packaging
Flexographic printing remains a cornerstone of the packaging industry, particularly for high-volume production runs. This versatile printing method uses flexible relief plates to transfer ink onto various substrates, including paper, plastic, and metallic films. The technology has seen significant improvements in recent years, with advancements in plate materials, ink formulations, and press designs contributing to enhanced print quality and efficiency.
One of the key advantages of flexographic printing is its ability to handle a wide range of substrates at high speeds. Modern flexo presses can achieve production rates of up to 600 meters per minute, making them ideal for large-scale packaging operations. Additionally, the use of quick-drying inks allows for faster turnaround times and reduced waste.
Improvements in plate technology have also played a crucial role in enhancing the capabilities of flexographic printing. The introduction of high-definition flexo plates has enabled printers to achieve finer details and smoother gradients, rivaling the quality of offset printing in many applications. This has expanded the use of flexo printing into premium packaging segments that were previously dominated by other printing methods.
Furthermore, the integration of automated color management systems and inline quality control measures has significantly reduced setup times and improved consistency across print runs. These advancements have made flexographic printing an increasingly attractive option for brands looking to balance cost-effectiveness with high-quality output in their packaging production.
Digital inkjet systems for variable data labeling
While flexography excels in high-volume production, digital inkjet systems have revolutionized the world of variable data labeling and short-run packaging. These systems offer unparalleled flexibility, allowing for on-demand printing of customized labels and packaging with minimal setup time. The ability to print variable information, such as batch numbers, expiration dates, and personalized content, has made digital inkjet technology indispensable in industries ranging from food and beverage to pharmaceuticals.
Digital inkjet systems utilize a non-contact printing method, where tiny droplets of ink are precisely deposited onto the substrate. This technology enables printing on a variety of materials, including heat-sensitive films and textured surfaces, which can be challenging for traditional printing methods. The absence of printing plates also means that design changes can be implemented quickly and cost-effectively, making digital inkjet ideal for prototyping and market testing of new packaging designs.
HP Indigo digital presses for short-run label production
HP Indigo digital presses have become a go-to solution for short-run label production, offering offset-quality prints with the flexibility of digital technology. These presses use liquid electrophotography (LEP) technology, which combines the versatility of digital printing with the smooth laydown and vibrant colors typically associated with offset lithography.
The HP Indigo platform supports a wide range of substrates, including pressure-sensitive labels, shrink sleeves, and flexible packaging materials. With features like spot color matching and variable data printing, these presses enable brands to create highly customized labels that stand out on store shelves. The ability to print on demand also helps reduce inventory costs and minimize waste, aligning with the growing emphasis on sustainable packaging solutions.
Epson SurePress for eco-solvent label printing
Epson’s SurePress line of digital label presses offers an eco-solvent inkjet solution for label printers seeking environmental sustainability without compromising on quality. These presses use water-based resin inks that produce vibrant, durable prints while reducing the environmental impact associated with solvent-based systems.
The SurePress technology is particularly well-suited for printing on uncoated papers and films, making it a versatile option for a variety of label applications. With features like automatic head maintenance and color management, these presses are designed to deliver consistent print quality with minimal operator intervention, enhancing productivity in label printing operations.
Xeikon CX500 for roll-to-roll digital label printing
The Xeikon CX500 represents the latest in roll-to-roll digital label printing technology, utilizing dry toner electrophotography to produce high-quality labels at impressive speeds. This press is designed for medium to high-volume label production, bridging the gap between traditional flexographic printing and short-run digital solutions.
One of the key advantages of the CX500 is its ability to print on a wide range of standard label substrates without the need for pre-treatment or coating. This versatility, combined with its food-safe toner technology, makes it an excellent choice for food packaging applications where regulatory compliance is critical. The press also offers enhanced color consistency and registration accuracy, ensuring that labels maintain their visual appeal across long production runs.
Thermal transfer printing for durable industrial labels
In industrial environments where labels need to withstand harsh conditions, thermal transfer printing has emerged as a reliable solution. This technology uses heat to transfer ink from a ribbon onto the label substrate, creating durable and long-lasting prints that can resist abrasion, chemicals, and extreme temperatures.
Thermal transfer printers are widely used for creating barcode labels, asset tags, and product identification labels in manufacturing and logistics settings. The technology offers several advantages, including:
- High print resolution for crisp text and scannable barcodes
- Compatibility with a wide range of label materials, including polyester and polypropylene
- On-demand printing capabilities for just-in-time label production
- Low maintenance requirements compared to other industrial printing technologies
Recent advancements in thermal transfer technology have focused on improving print speed and reducing ribbon consumption. Some modern thermal transfer printers now incorporate near-edge printheads that allow for faster printing and more efficient use of ribbon material, reducing operational costs and environmental impact.
Gravure printing for premium packaging applications
While digital and flexographic technologies have gained significant ground in recent years, gravure printing remains the method of choice for premium packaging applications that demand the highest level of print quality and consistency. Gravure printing uses engraved cylinders to transfer ink onto the substrate, resulting in exceptionally smooth and detailed images.
The gravure printing process excels in reproducing fine details, subtle tonal gradations, and metallic effects, making it ideal for high-end cosmetics packaging, luxury goods, and premium food and beverage labels. The ability to print on a wide range of substrates, including flexible films and foils, further expands its applications in the packaging industry.
While traditionally associated with long print runs due to the high cost of cylinder engraving, recent innovations in cylinder making technology have made gravure more accessible for shorter production runs. Laser-engraved cylinders and direct laser engraving systems have reduced setup times and costs, allowing gravure to compete more effectively with other printing methods in the mid-range packaging market.
Sustainable printing solutions for eco-friendly packaging
As environmental concerns take center stage in consumer preferences and regulatory landscapes, the packaging industry is increasingly focusing on sustainable printing solutions. This shift towards eco-friendly practices encompasses various aspects of the printing process, from ink formulations to substrate choices and waste management strategies.
Water-based ink systems for reduced environmental impact
Water-based ink systems have gained popularity as a more environmentally friendly alternative to solvent-based inks. These inks offer several advantages in terms of sustainability:
- Lower volatile organic compound (VOC) emissions during printing and drying
- Reduced hazardous waste generation and easier disposal
- Improved workplace safety due to the absence of harmful solvents
- Enhanced recyclability of printed packaging materials
Advancements in water-based ink technology have significantly improved their performance on non-porous substrates, expanding their use in flexible packaging applications. Some modern water-based inks can now achieve adhesion and durability comparable to solvent-based alternatives, making them a viable option for a wider range of packaging products.
UV-LED curing technology for energy-efficient printing
UV-LED curing technology represents a significant advancement in energy-efficient printing processes. Unlike traditional UV curing systems that use mercury lamps, UV-LED systems offer several environmental and operational benefits:
UV-LED curing systems consume less energy, reducing the carbon footprint of printing operations. They also generate less heat, allowing for printing on heat-sensitive substrates and reducing cooling requirements in production facilities. Additionally, the longer lifespan of LED bulbs compared to mercury lamps results in reduced waste and lower maintenance costs.
The instant on/off capability of UV-LED systems eliminates warm-up and cool-down periods, further enhancing energy efficiency and productivity. This technology has been successfully implemented across various printing methods, including flexography, inkjet, and screen printing, contributing to more sustainable packaging production processes.
Biodegradable and compostable substrate options
The development of biodegradable and compostable packaging materials has opened new avenues for sustainable printing solutions. These substrates are designed to break down naturally under specific environmental conditions, reducing the long-term impact of packaging waste on ecosystems.
Printing on biodegradable substrates presents unique challenges, as the inks and coatings used must not interfere with the material’s ability to decompose. Specialized ink formulations have been developed to address these requirements, ensuring that the entire packaging system remains environmentally friendly.
Some examples of biodegradable and compostable substrates gaining traction in the packaging industry include:
- PLA (Polylactic Acid) films derived from renewable resources like corn starch
- Cellulose-based materials that mimic the properties of conventional plastics
- Paper-based substrates with biodegradable coatings for moisture resistance
As printing technologies continue to evolve, manufacturers are developing new solutions to optimize print quality and adhesion on these eco-friendly materials, ensuring that sustainability does not come at the cost of packaging performance or visual appeal.
Closed-loop recycling systems for print waste management
Implementing closed-loop recycling systems in printing facilities represents a significant step towards sustainable packaging production. These systems aim to minimize waste and maximize resource efficiency by reprocessing and reusing materials within the production cycle.
In the context of industrial printing, closed-loop recycling can involve:
- Recovering and reprocessing waste ink for reuse in production
- Recycling printing plates and cylinders to recover valuable materials
- Implementing solvent recovery systems to reduce VOC emissions and material costs
- Utilizing waste paper and substrate trimmings as raw materials for new packaging products
By adopting closed-loop recycling practices, printing facilities can significantly reduce their environmental footprint while often realizing cost savings through improved resource utilization. These systems also help companies meet increasingly stringent environmental regulations and demonstrate their commitment to sustainability to environmentally conscious consumers.
Quality control and inspection systems in industrial printing
Ensuring consistent print quality and accuracy is crucial in industrial packaging and labeling applications. Modern quality control and inspection systems play a vital role in maintaining high standards throughout the printing process, minimizing waste, and preventing defective products from reaching the market.
Advanced vision systems equipped with high-resolution cameras and sophisticated image processing algorithms can detect a wide range of print defects in real-time. These systems can identify issues such as color variations, registration errors, missing print, and substrate defects at production speeds, allowing for immediate corrective action.
Inline spectrophotometers and color management systems enable continuous monitoring and adjustment of color accuracy during print runs. This ensures that packaging colors remain consistent across different production batches and printing technologies, maintaining brand integrity and product recognition on store shelves.
For applications requiring precise variable data printing, such as barcodes and QR codes, specialized verification systems can be integrated into the production line. These systems check the readability and accuracy of printed codes, ensuring that they meet industry standards and regulatory requirements.
The integration of these quality control and inspection systems with print management software and production databases allows for comprehensive tracking and reporting of print quality metrics. This data-driven approach enables continuous improvement of printing processes, helping manufacturers optimize their operations and deliver consistently high-quality packaging solutions to their customers.